Automation is Not One Size Fits All
A Continuation of the Series: Automation Is
February 03, 2022
Not all automated warehouses are built the same. Understanding our customers’ needs and organizational outcomes are essential to adding the right amount and types of automation to our facility. Fundamentally, there are three broad approaches to automation as it applies to integration into the cold chain.
The fully automated warehouse.
The fully automated warehouse is a facility run by large scale, fully integrated robotic systems, outfitted with numerous cranes and rows of conveyors for inbound receiving and pallet building. While there will always be a supervisory human component in any facility, 95% of our fully automated warehousing is no-touch.
These new warehouse builds, combined with our algorithms and software, allow for major increases in storage density, throughput and capacity. As a benefit, these facilities are not encumbered by the height restrictions that forklifts impose on manual warehouses. Taller building heights provide flexibility in where we can locate a warehouse, including heavily populated areas.
Lineage Automation in Action: Bergen op Zoom
With a throughput of 5,500 inbound and outbound pallets per day and a maximum storage capacity of 180,000 pallets, our Bergen op Zoom, Netherlands, facility provides a glimpse into the future of cold chain automation. Bergen op Zoom only has 15 forklift drivers per shift.
The Bergen op Zoom facility came into being as a result of our relationship with a European commodity producer. Coordinating with our partner, we developed an electronic data interchange (EDI) that, when married with our warehouse management system software and then received by our I-point (inspection point), allows for a fully automated process from inbound truck to outbound truck.
We achieve such incredible throughput with approximately 100 team members, including one process controller. Acting essentially as a warehouse air traffic controller, the process controller is responsible for ensuring that the thousands of pallet positions on the expansive system of conveyors throughout the warehouse are synchronized properly. When a disruption occurs, it’s the process controller’s job to ensure that there’s no delay for the customer.
As automated processes scale and can build from other processes, Bergen op Zoom will one day be able to increase the overall storage capability to 280,000 pallet positions. Dedicated buildings such as the Bergen op Zoom facility can apply customized automation, specifications, designs and workflows based on a customer’s specific needs. The design specifications of a dedicated facility are a much less speculative exercise.
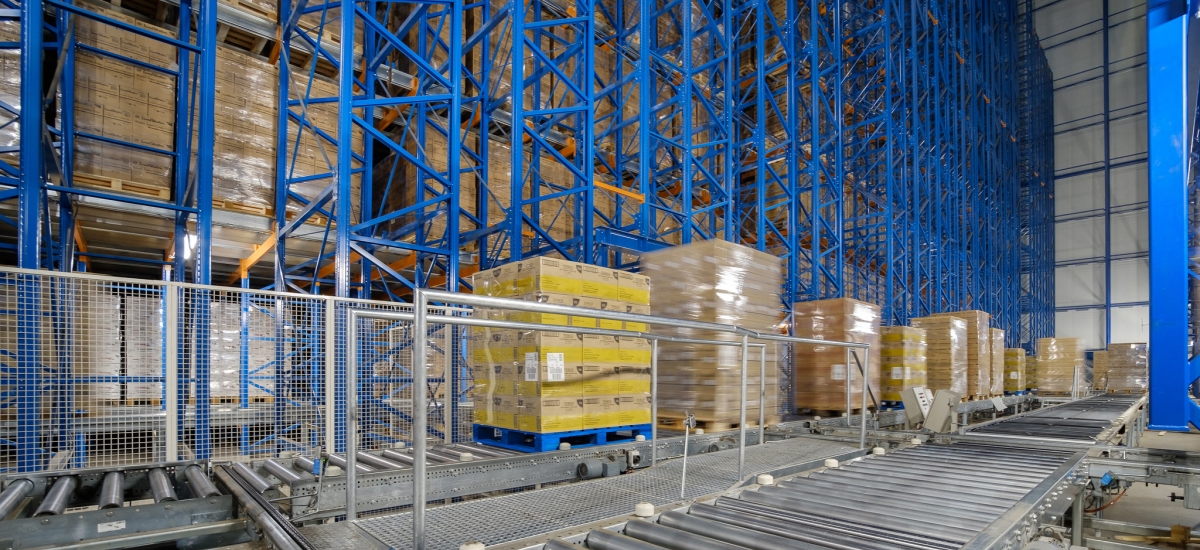
A mixed-mode approach.
Not all organizations can afford to invest in building new, fully automated structures. Retrofitting existing buildings with different modes of automation offers many of the same benefits at a lower cost. Mixed-mode automation is a combination of human-dependent tasks with an automated component. Mixed mode can help warehouses struggling with labor and throughput issues by automating processes without disrupting overall operations.
Successfully designing mixed-mode automation requires looking at every task and every workflow as a programmable function. Regardless of the human or automated component, workflows can be mapped out and synthesized through this process. The right software can determine functions that are greatest served by converting to an automated process.
Lineage Automation in Action: Allentown, Pennsylvania
As a testing ground for mixed mode, Lineage decided to reengineer a section of our Allentown, Pennsylvania facility. As a large regional distribution center for several customers, Allentown moves approximately 200 trucks of product in and out daily, encompassing nearly 4 million pounds per day. In addition to the impact of labor shortages felt across the industry, customers have added more choices/SKUs to their offerings, and, in turn, consumers have become more specific in their orders. This growth in order variability has significantly increased the amount of case picking or partial pallets needed to fulfill orders.
The case picking function is traditionally a very manual and very slow process that consumes a great deal of labor. To alleviate the stress of new demands, we are implementing automation throughout the warehouse. More specifically, we are utilizing a layer-picker machine and multiple AGVs (automated guided vehicles) to reduce the amount of labor utilized in the case picking and full-pallet movement function.
The layer picker and the AGVs will work as part of the overall inbound/outbound flow of product. Humans on MHE (material handling equipment) will continue to load and unload trucks. AGVs will automatically retrieve inbound pallets from staging areas on our dock, put into and pull pallets out of racking, feed the layer picker with the needed product and place outbound pallets in staging areas on the dock. The layer picker will replace the human element of case picking for tens of thousands of cases each day.
By implementing select automated capabilities, we anticipate numerous benefits, such as reduced labor hours, improved safety, improved quality and improved customer service. We also expect to minimize the errors caused by incorrect picking of product. Lastly, with a consistent automation presence, our fluctuations in service should decrease as we are less at risk of labor shortages driving decreases in service.
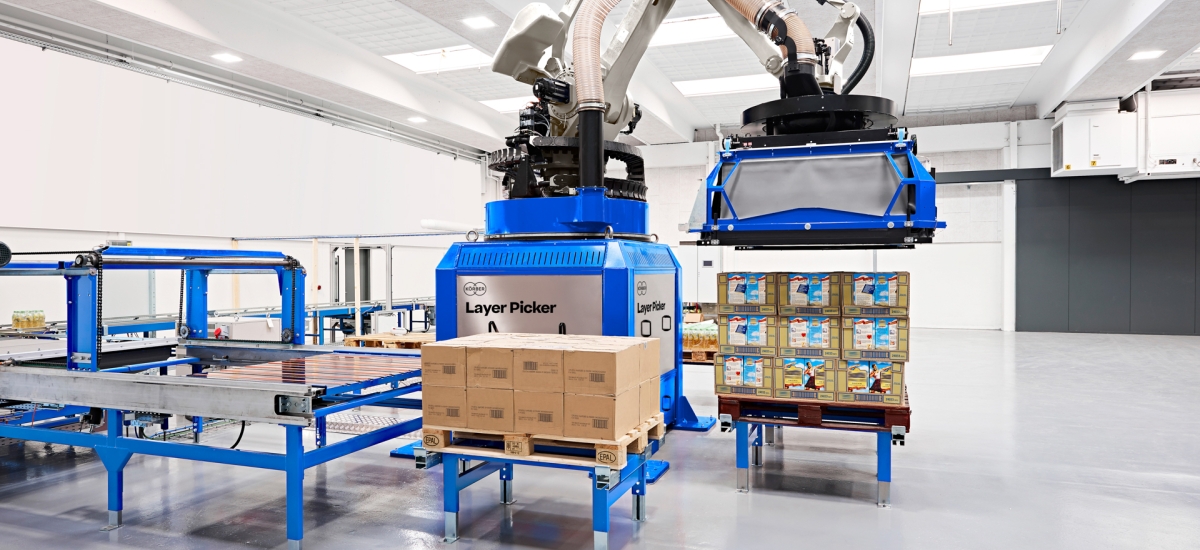
Selectively adding to existing processes.
Automation levels (i.e., the amount of automation in a warehouse) are set based on the tasks that need to be done. Those tasks are dictated by the customers being served, so automation designs need to be built to anticipate customers, market needs and supply chain movements.
Any automated application ultimately reduces workflow. In an automated work environment, at a moment’s notice, we can lessen automated functions, but technological capabilities and equipment capacity constrain our ability to add functions. Traditionally, more work simply meant more labor, but with automation, there’s a ceiling. There are only so many moves per hour that a given set of hardware can perform; so, before implementing any automated process, we need to understand the workflow and limitations.
Choosing the best approach.
Automation is a service that will ultimately change the future of the cold chain. Among the numerous beneficial aspects of automation is the amount of flexibility it allows on our warehouse floor. While individual aspects of automated systems are designed to do one specific task, the concept of automation allows for countless combinations of individual tasks to enable large-scale applications. The best way to implement automation across the global cold chain environment is to consider the basic fundamental differences of each level and how it will affect efficiency and operations.
Click here to read the rest of the series: Automation Is.