Introducing Libra: The Lineage Algorithm Optimizing How We Load Trucks
May 07, 2025
Supply chain professionals know that every detail matters in the cold chain and even seemingly small disruptions – like a minor transportation delay – can have an outsized ripple effect. That’s why they focus on optimizing processes, managing costs and mitigating supply chain risks to protect the flow of their goods.
At Lineage, these same objectives drive us to rethink the way the food supply chain works while striving for greater efficiency at each step. For example, Lineage warehouse operators face the complex task of loading products onto trucks efficiently, playing real-world Tetris with pallets of varying sizes and weights every day. In automated facilities, where dock space is limited, this presents an even greater challenge. This very problem led to our Data Science team creating Libra – our patented algorithm for optimizing truck loading.
The Challenge: Optimizing Outbound Truck Loading
Loading outbound trucks is a critical step in cold chain warehousing operations, but it's often difficult. It requires an experienced operator, valuable time and physical space to handle each pallet and stage orders. Adding complexity to the process, operators must factor in multiple variables including pallet heights and weights. Since trucks are often filled with more pallets that can fit on the floor of the truck, operators may need to determine which pallets can be stacked on one another. Additionally, the pallets’ weight must be distributed evenly over the trailer sides and axles. They might also have to account for how the orders will be off-loaded, if there are orders bound for multiple destinations – like a retailer’s stores or regional distribution centers – consolidated within a single truck.
Imagine an operator on the warehouse dock carefully planning how to load a customer's order onto a truck. Each pallet has different weights, sizes and even destinations. Finding the perfect arrangement to fit as much product as possible in the truck is like solving a complex puzzle. On top of that, the operator must move quickly – after all, every second counts in the cold chain and more trucks are lining up to receive their orders. This challenge is exactly what Libra was designed to take on.
The Solution: Libra
To simplify this process of figuring out how and where each pallet should be placed within a truck, Lineage’s Data Science team created Libra. Libra is an algorithm designed to optimize the process of loading pallets of temperature-sensitive products onto refrigerated trucks that keep them cool on their journey.
Libra receives pallet and vehicle information for outbound loads and determines an optimal loading arrangement based on specific requirements, including the dimensions of the truck and vehicle and axle weight limits. The algorithm then performs a series of complex calculations to find possible solutions and selects an optimal solution to guide the loading process. Think of Libra like playing a life-sized game of Tetris. The pallets are rotated, shifted and stacked efficiently to achieve the best arrangement for each truck.
The Libra algorithm models the time required for various loading tasks to determine the optimal loading style. It considers factors such as the time to stack a pallet, turn a pallet sideways, load a stack of pallets and bring pallets out of the freezer. All of this is done while adhering to height and weight restrictions, as well as dock and conveyor space boundaries.
How Libra Works
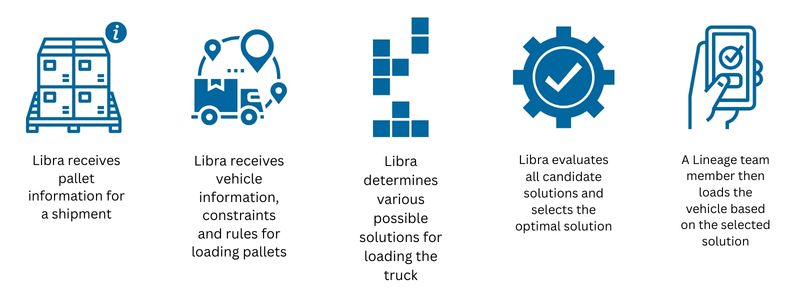
The Results: Saved time, saved labor and saved resources
Libra optimizes the loading of pallets onto vehicles, which can provide several benefits to our customers.
- Time Savings: Libra reduces the time it takes to load trucks. This leads to faster turnaround times and more efficient operations.
- Labor Optimization: Since Libra provides the instructions for loading the truck, our operators don’t need to stage all the outbound product on the dock at the same time nor do they have to spend time inspecting the staged pallets to determine how to load the truck.
- Fuel Savings: By determining an optimal loading arrangement, Libra allows more product to be loaded per truck, reducing the number of trips needed to transport the same amount of product and saving fuel.
- Space Optimization: Less space needed to stage orders reduces overall traffic congestion on the dock – this is particularly beneficial for facilities with rail access, which requires significant dock space for loading and unloading – and improves overall safety for our team members.
By cutting the time spent planning, arranging and rearranging pallets, warehouse operators can quickly clear docks, reducing congestion and allowing team members to focus on other high-value tasks.
Developing & Deploying Libra
The development of Libra is a testament to the expertise and problem-solving skills of our Data Science team. Peter Greskoff, Senior Data Scientist, played a major role in the Libra project. Peter’s background in electrical engineering and experience developing software gave him a unique perspective in optimizing this innovative solution.
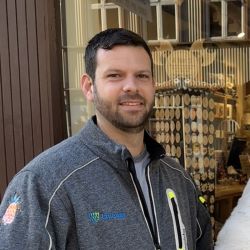
“There’s no substitute for an experienced operator when it comes to packing a truck. Our goal is to leverage technology to make the same decisions a veteran team member would make much sooner in the shipment process, without requiring staging of the products being loaded. This helps us make the supply chain more efficient and helps our team members,” said Greskoff. “This creates a safer, less crowded dock space, helps our team members, and allows us to make the supply chain more efficient.”
Libra was first successfully piloted at our automated cold storage warehouse in Sunnyvale, TX and has since been implemented at select automated facilities. Our team is now planning a pilot program for Libra implementation at a conventional warehouse in late 2025. We hope to achieve some of the same benefits realized in our automated sites by utilizing Libra within our manual operations. Stay tuned for updates on this project!
Visualizing Libra in Action
Seeing Libra’s algorithm in action helps bring clarity to just how impactful this innovation can be in real-world situations. Here are two visual examples that illustrate Libra’s novel ingenuity in maximizing truck space and warehouse efficiency:
Example 1: This visualization shows the arrangement of pallets in a truck, with the thin bronze areas representing the wooden pallets holding the product.
Different colors correspond to different stops. The red represents product for the truck’s first stop and are loaded at the back of the truck closest to the loading doors, while the teal represents the second stop, and purple represents product on the truck’s last stop.
Libra also determines which pallets should be stacked to optimize space, as shown by the multiple vertically stacked pallets. The bottom half of the visualization shows the total weight at each position in the truck.
Example 2: This example illustrates how Libra determines the orientation of pallets in the truck.
While loading all pallets straight in is simpler, it limits the truck to 24 positions in a standard 53-foot reefer truck. In the first example, loading all pallets sideways allows for 30 positions. The second example shows Libra’s suggestion to alternate straight and sideways loading (a “pinwheel” load), which allows for 28 positions.
Innovating to Build a Better Cold Chain
Libra is a fantastic example of cold chain innovation solving for real-world problems and showcases how innovators like Pete and the Lineage Data Science team are helping us build a better cold chain. In the future, we hope to integrate the Libra algorithm into the customer ordering process. This can help supply chain professionals make informed decisions by providing greater visibility into how product orders fit onto trucks as they are placing their orders.
Moreover, Libra represents another milestone in our ongoing innovation journey that includes our 100th patent, Lineage Link, energy innovations and expansions to our automated facility network. And we’re just getting started. Our team members continually look for ways to improve our operations so we can deliver more value for our customers and achieve our purpose – transforming the food supply chain to eliminate waste and help feed the world.