Lean Principles in Action: A Kaizen Event Snapshot with Lineage Dallas
May 15, 2025
At Lineage, continuous improvement is more than just a concept, it's a core part of how our teams operate across our global network. We strive to inspire a culture of ownership where our team members feel like they can take charge of the work they do every day and make improvements to the processes they rely on.
One way that our teams put this mindset in motion is by hosting Kaizen events, part of the lean management methodology, designed to map out potential process changes. These collaborative improvement efforts give our team members the opportunity to take ownership of their work, engage in problem-solving and directly impact operational efficiency while keeping the world’s food supply chain moving.
Using Kaizen, Lean & Continuous Improvement to Make a Difference
Kaizen, which originated in post-World War II Japan, is contemporarily known as a lean management technique focused on making incremental changes to drive better performance through collaborative problem-solving sessions. By zooming in on a singular pain point, our team members can work together to create a solution. Whether tackling large operational challenges or improving small, everyday processes, Kaizen helps teams tailor solutions to their unique needs. Recently, the team at our Dallas Dynasty facility hosted a Kaizen event designed to streamline their inbound receiving process. Their ambitious goal? Cut the average truck receiving time by more than half.
From Problem to Process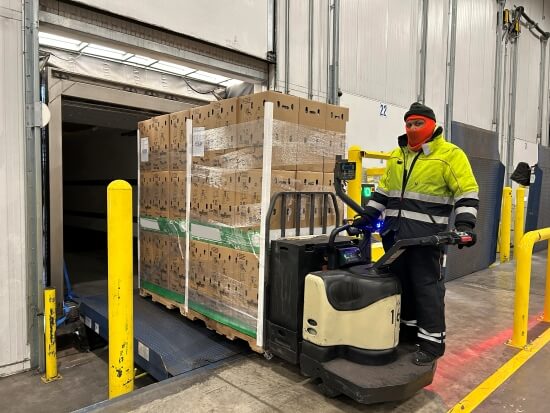
For the receiving team at Dallas Dynasty, dock congestion was a persistent challenge. With limited space to stage inbound loads and a constant flow of new trucks arriving, team members often found themselves overwhelmed amidst the constant commotion. Regardless, they worked hard to maintain on-time service but felt that the current process left a lot to be desired.
Deciding that enough was enough, the team decided to hold a Kaizen event to better understand and address the issue. Together, they created a Value Stream Map to visualize the current state of their receiving process. This map revealed some eye-opening data: each inbound load took about 117 minutes to complete, and at peak times up to 133 pallets were staged on the dock waiting to be put away.
Clearly identifying the waste was a major turning point. Through their mapping, the team found that their largest inefficiency was the sequential nature of their process—unload, receive and put away—each done one step at a time, leading to disruptive dock congestion. By reimagining the process to eliminate staging—pallets were unloaded, processed and moved to the freezer all in one fluid step—they removed a massive source of waste from their day-to-day operations, driven by the hard work and creative ideas of the Dallas Dynasty team.
“It’s a lot simpler and a lot safer now,” says Roy Stewart, the Assistant General Manager. “Things are a lot more accessible…it’s very beneficial to everyone.”
The Results: Efficiency and Empowerment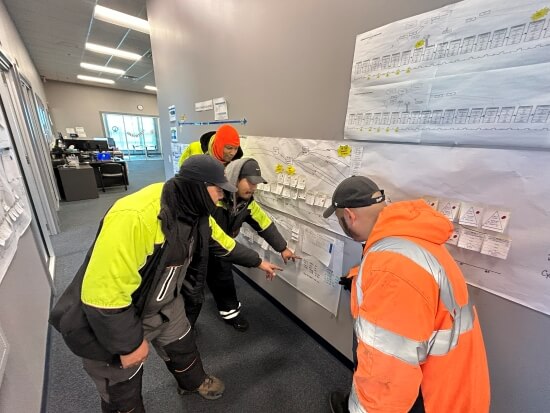
After their successful experiment, the team piloted the new workflow, testing and adjusting the process as necessary before officially implementing their new Just-In-Time procedure.
The impact was immediately apparent, with the time required to process an inbound truck dropping from 117 minutes to just 22 minutes. Even better, dock congestion was eliminated, with no more than four pallets staged at a time, allowing for easier flow and more consistent product temperatures.
This change delivered incredible, tangible results along with improved workflow. The team can now turn 2–3 trucks in the same time that it previously took to process one, effectively increasing throughput and revenue without adding additional labor.
According to Kaizen Team Leader, Tino Samreth, “[We’re] working in teams to get more trucks out and more trucks in using the same number of people. We’re not as rushed with the new process, and we can increase revenue at the same time.”
It's a textbook example of continuous improvement principles in practice—and a major win for the Dynasty team.
Continuous Improvement Across Lineage
Continuous improvement is an integral component of our culture here at Lineage. By focusing on our shared value of innovation, we encourage our global team to consistently deliver value for our communities and customers in all we do. As part of our global Lean mindset, Dallas Dynasty isn’t alone in their journey—facilities across the Lineage network are currently working on their own stories of continuous improvement, with Kaizen events being but one tool in that toolbox.
Right now, more than 60 facilities have started their Lean journey, with 94% of those facilities having been certified—with more on the way! Together, these sites then share their learnings and best practices outward across the network to foster continuous improvement in all aspects of the cold chain.
Moreover, we are proud to incorporate Lean principles and methods into both our core operations and corporate support functions—helping us prioritize and focus our efforts to eliminate waste and drive value for our customers and the business. Continuous improvement is truly a way of life for the Lineage team.
Looking Ahead: A Culture of Ownership and Innovation
Kaizen events like this highlight the power of what our Lineage team can do when we work together—when our team members are empowered to take initiative and improve their work environment, everyone wins, from individuals and facility teams to the organization as a whole.
As Lineage continues to build a culture rooted in continuous improvement, we’re reinforcing the idea that innovation doesn’t just come from the top: it thrives on the front lines. The recent success at Dallas Dynasty is just one of many examples showing how small, thoughtful changes can lead to remarkable results.
Our journey of improvement never stops. With every Kaizen event, we’re not just refining our operations, we’re cultivating leaders, strengthening teams and building a better food supply chain.